T1
Torch was created in 2012 as a side project after I started commuting by bike across Los Angeles and quickly realized that traditional bike lights were too small and ineffective. The T1 was the first product I would manage from concept to production myself.
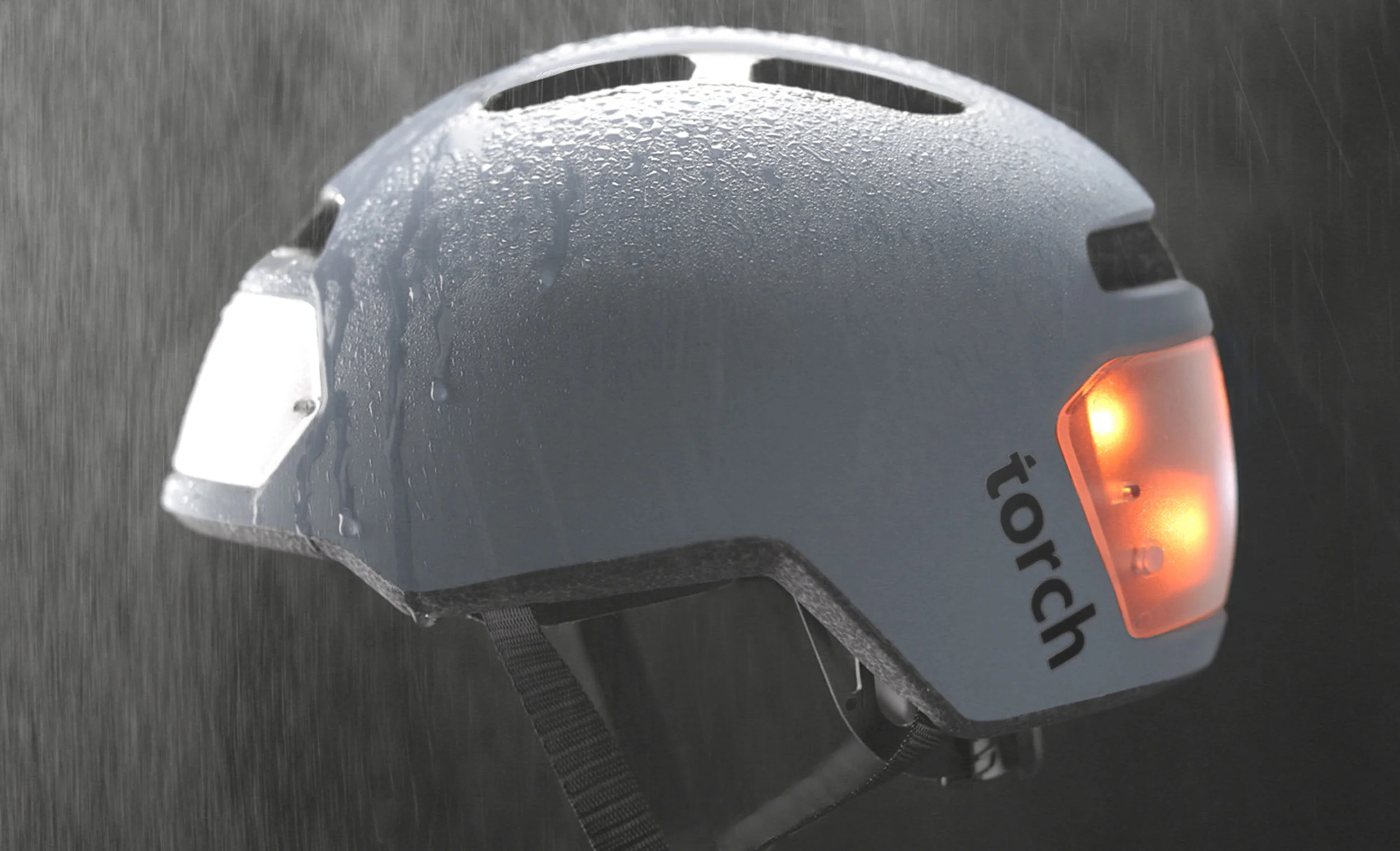
My goal with creating the Torch brand was to create cycling safety apparel that would not only make urban riders more visible during the night hours, but create products that would be seen as more stylish during the daylight hours. The helmet has been well received and has changed the industry by creating a market segment that quickly saw competition.
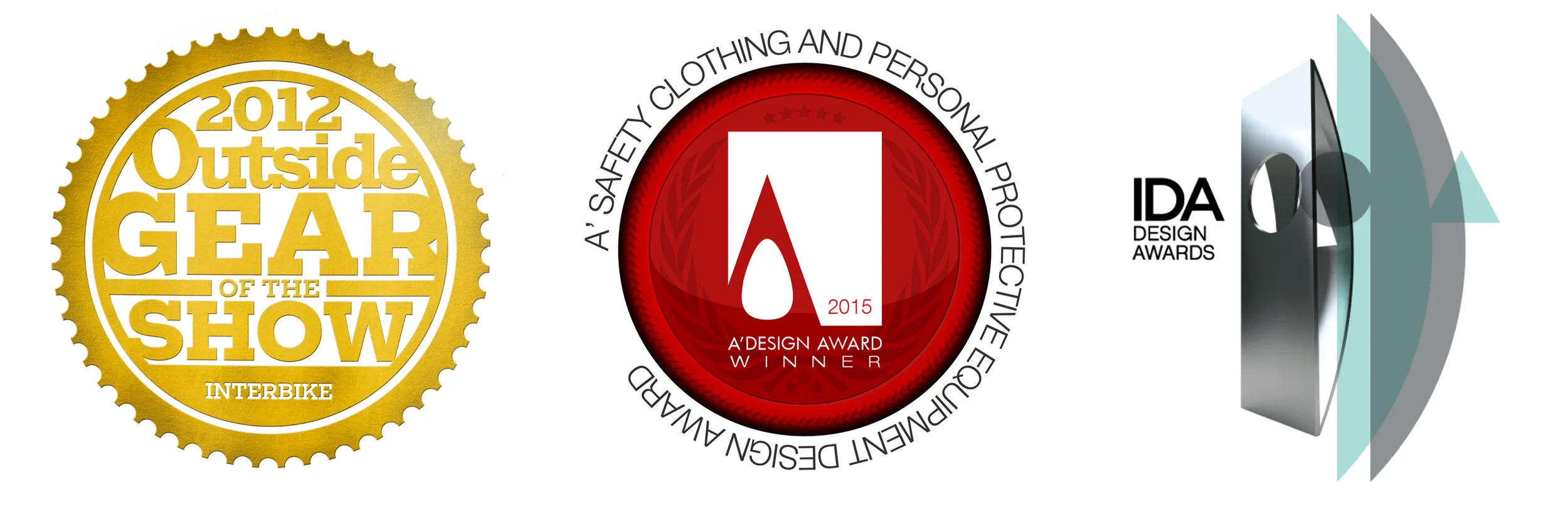
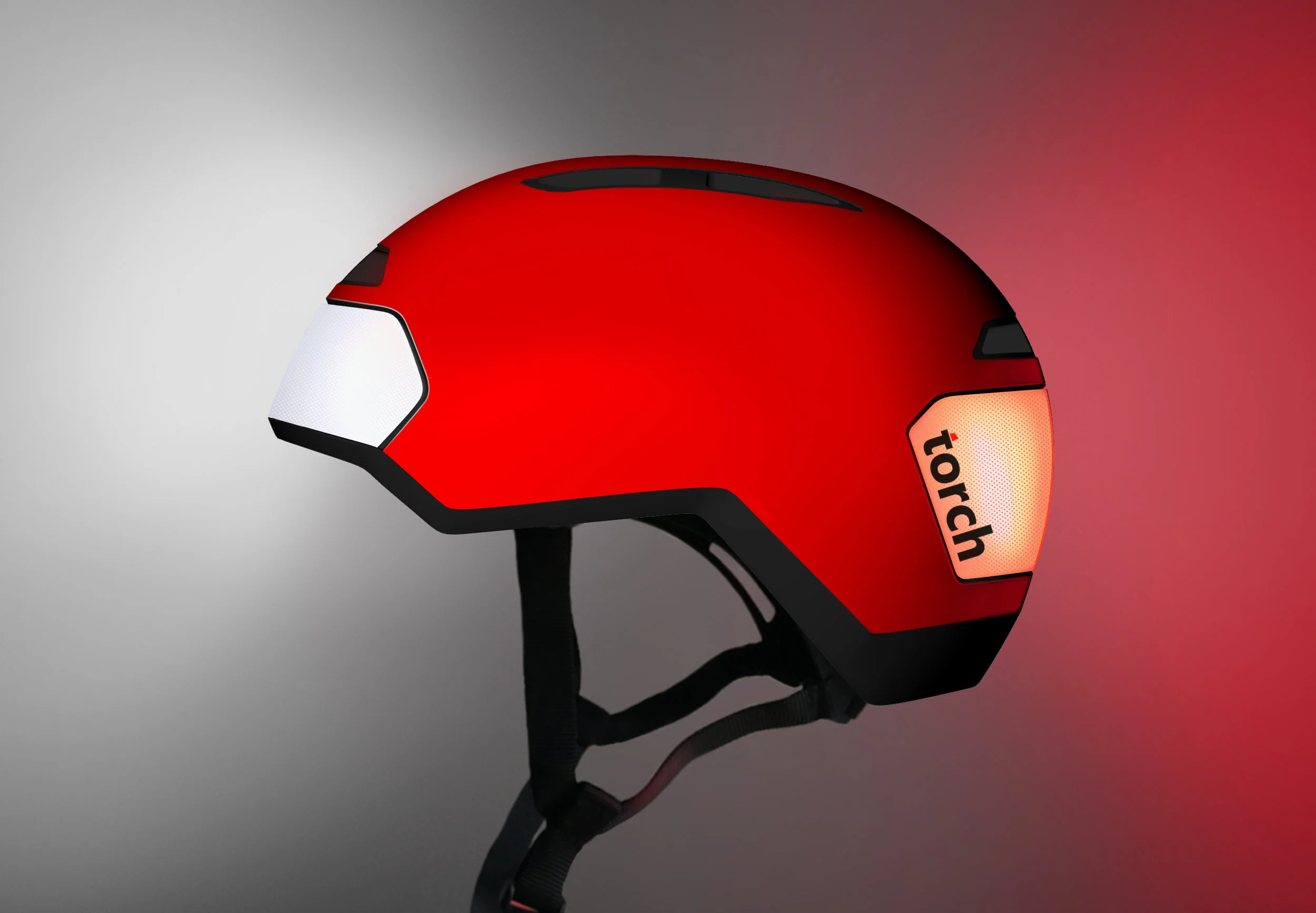
The concept for the T1 helmet was to integrate lights not only into the helmet, but into the profile of the helmet so as not to appear as an add on item. I wanted the helmet to have clean lines and minimal, properly placed, vents giving it a less sporty and more urban commuter style.
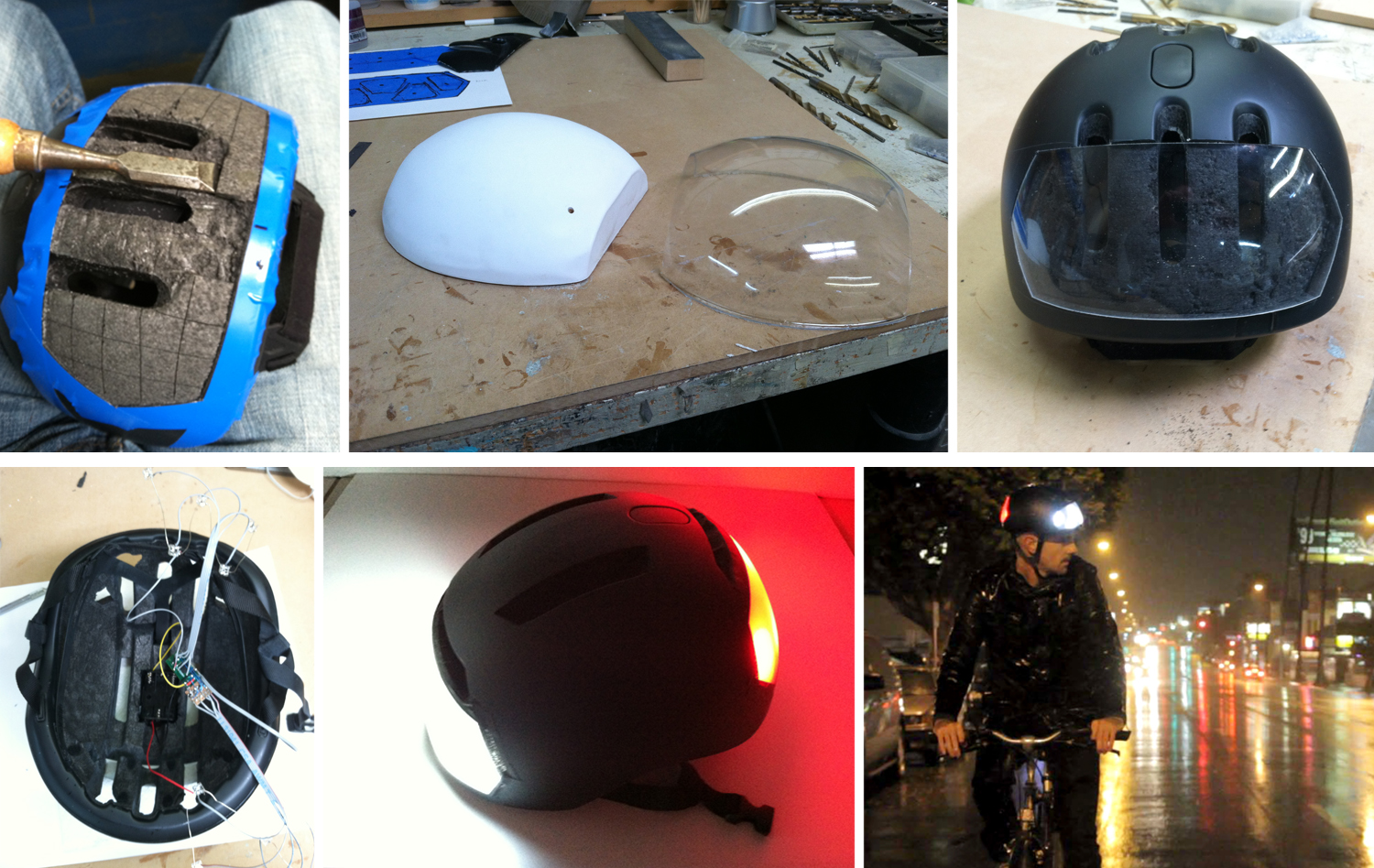
Existing products along with some self made vacuum formed lenses were used to construct the first proof of concept prototype. This model was soon after used to raise funds via crowdfunding.
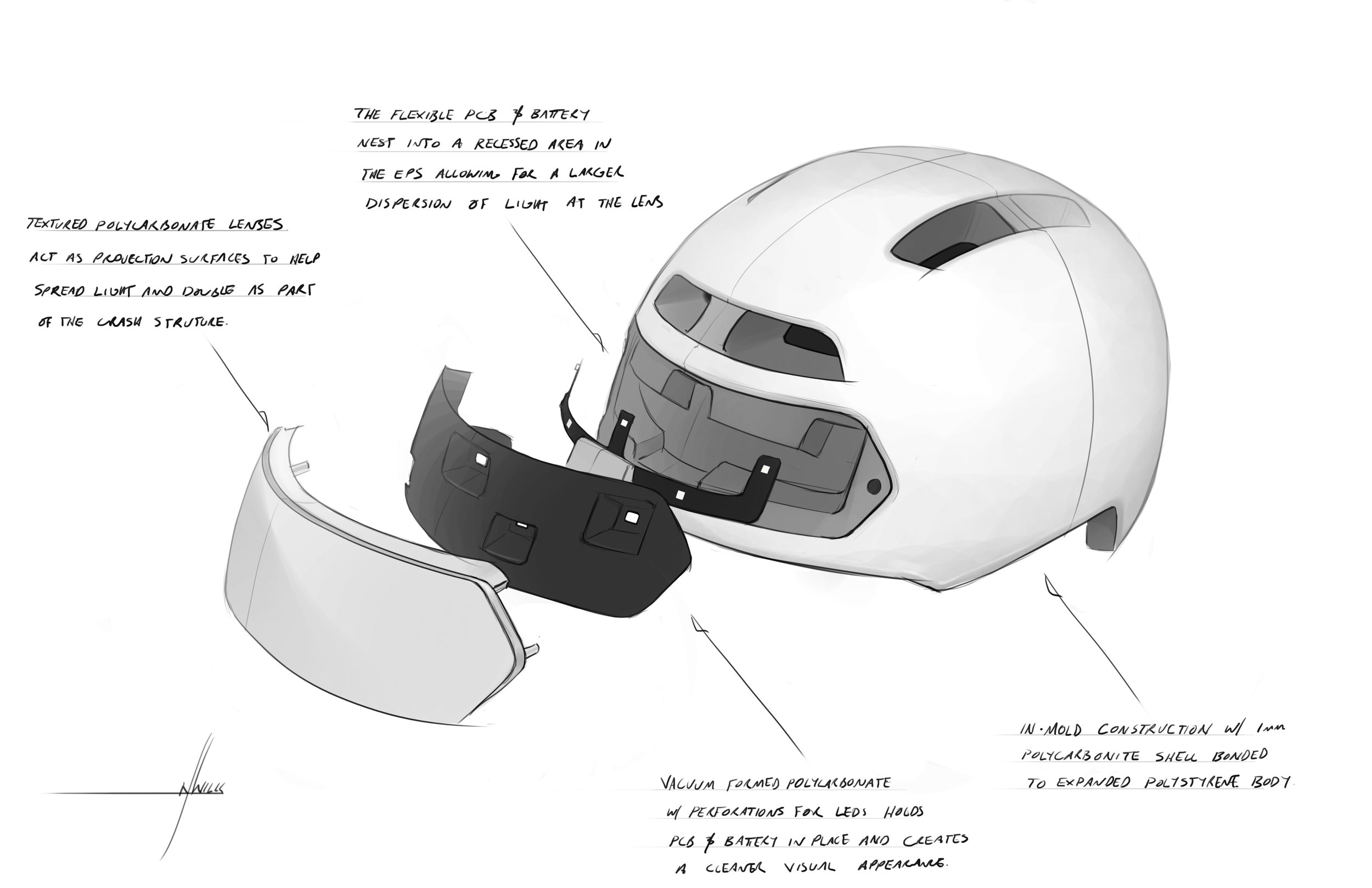
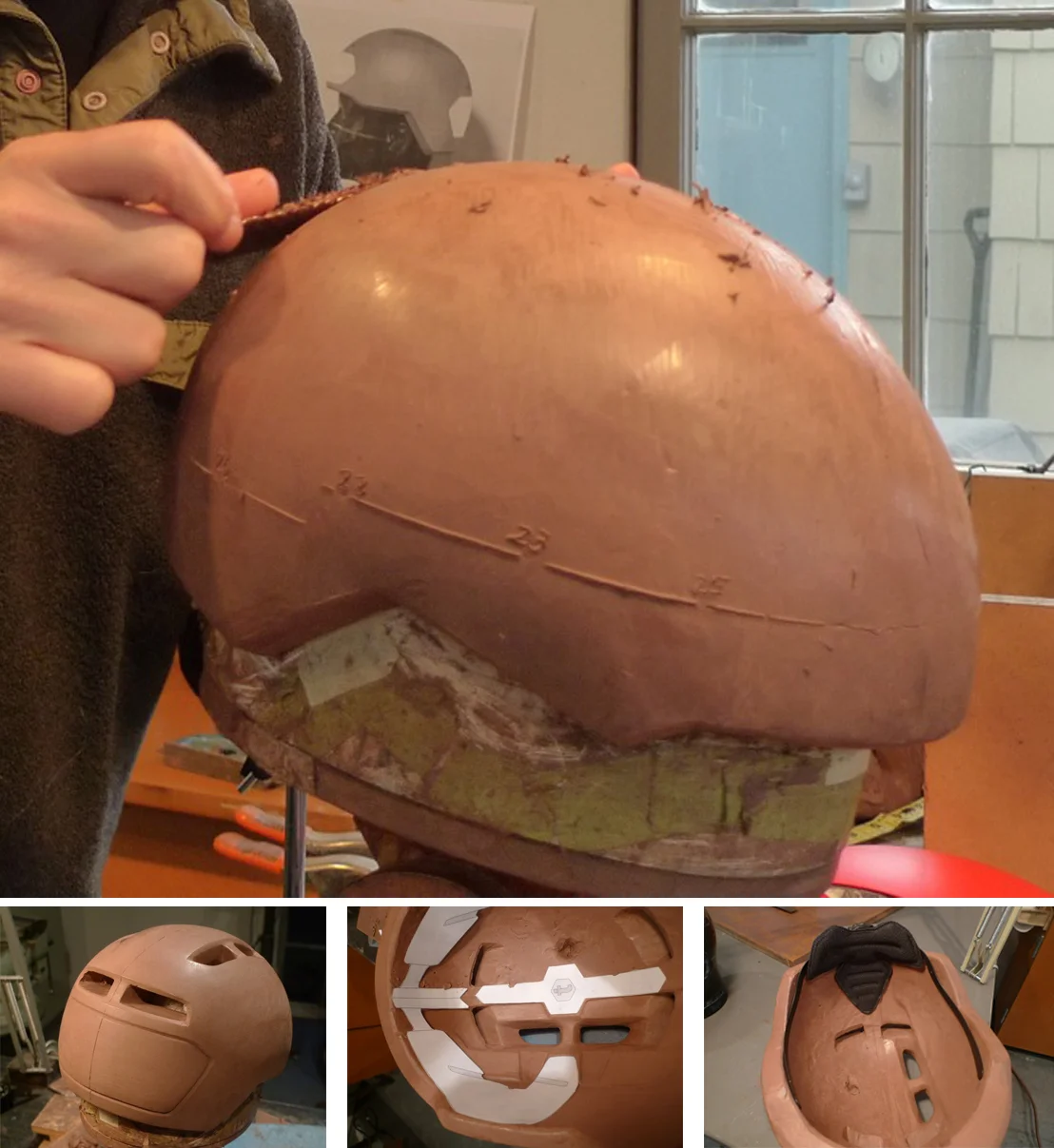
Post funding I collaborated with John Larkin, an experienced helmet designer, to finalize the production design. John not only has a wealth of knowledge when it comes to bike helmet design, but he had the necessary head form and tools needed to keep the project moving while I sourced manufacturing partners and worked with the electrical engineer to finalize the electronics. Although I would have loved to have done the clay myself, his final deliverable was on point and helped the project stay on schedule.

Keyshot was used to communicate the final production ready design and finish to the Kickstarter backers and were also useful when Entrepreneur Magazine came asking for images to include Torch in the Brilliant 100 issue!
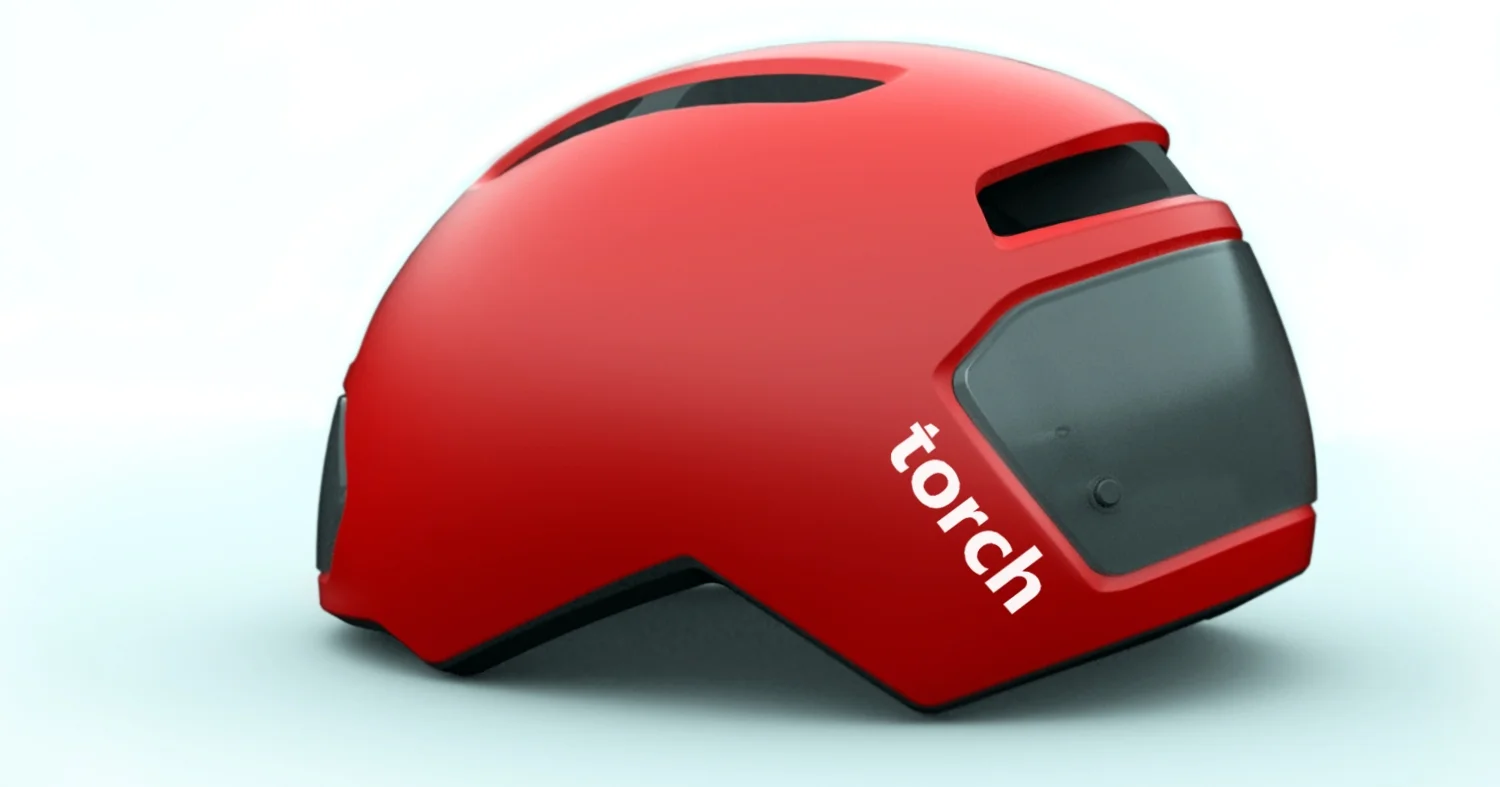
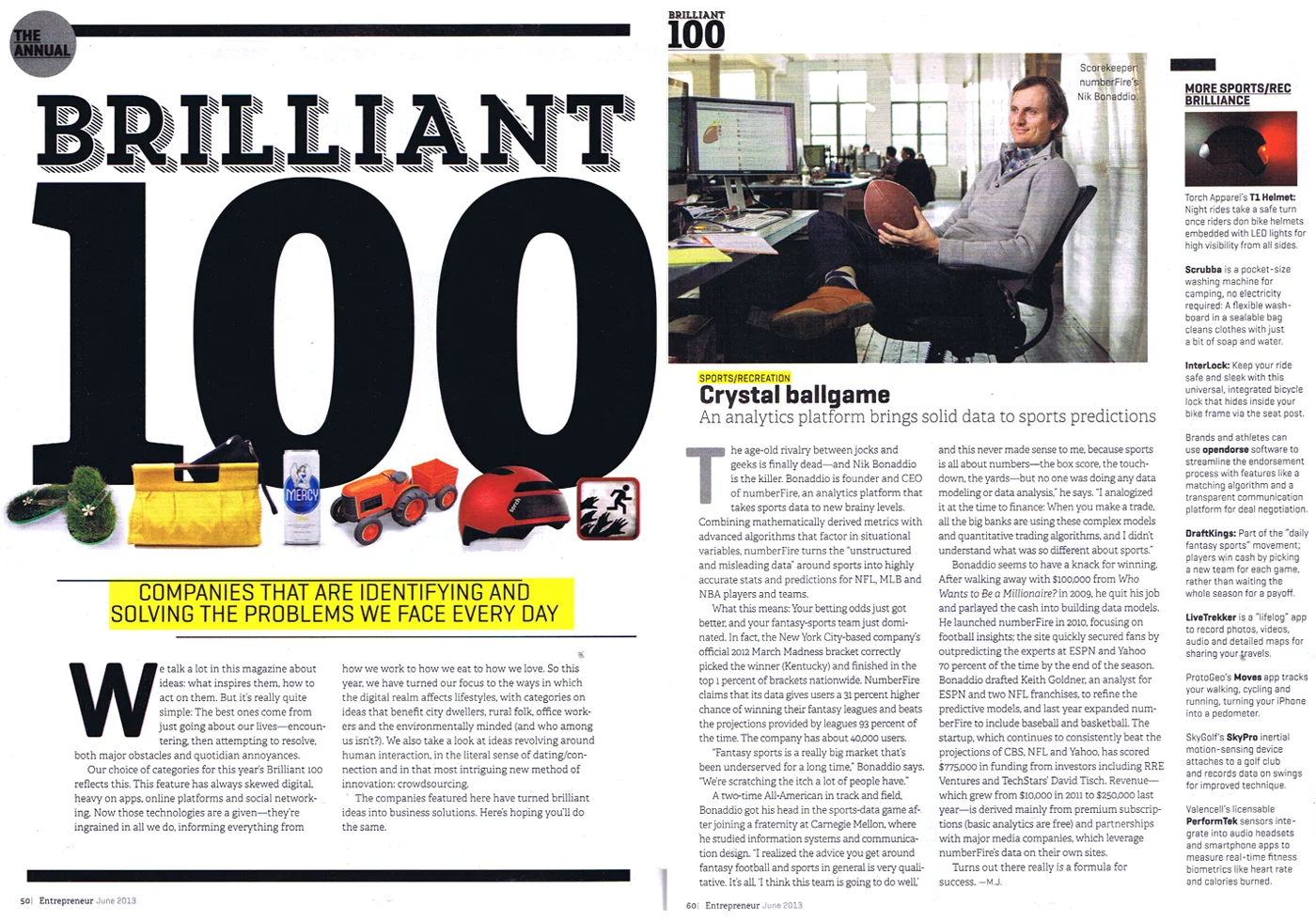
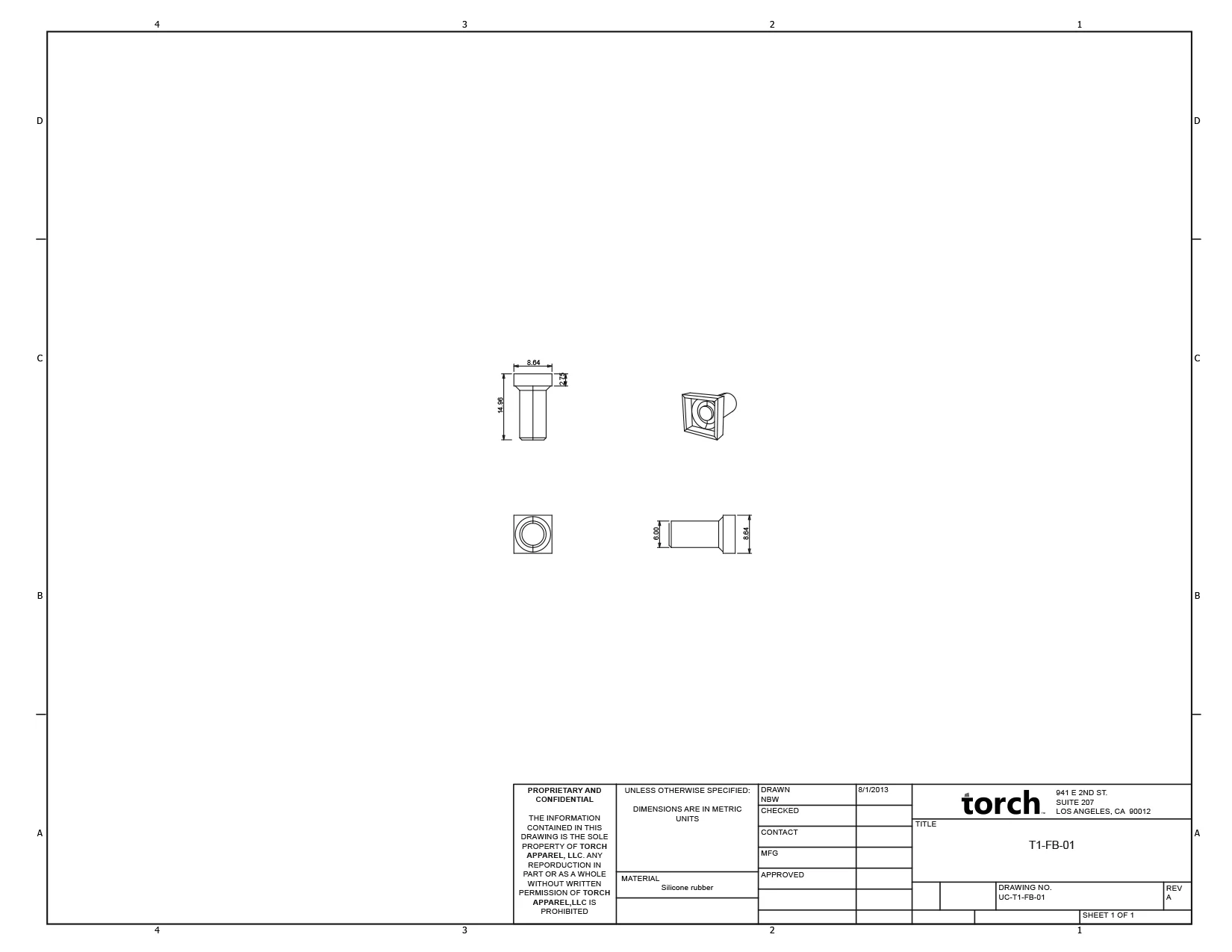
Since every part of this helmet was created specifically for this design even the smallest parts such as the rubber buttons had to be specified down to a fraction of a millimeter and tested across different materials to perform as intended. This button, for example, was tested in two different types of silicone and in 4 different shore durometers in order to offer just the right tactile feedback so the user can operate the lights without removing the helmet.
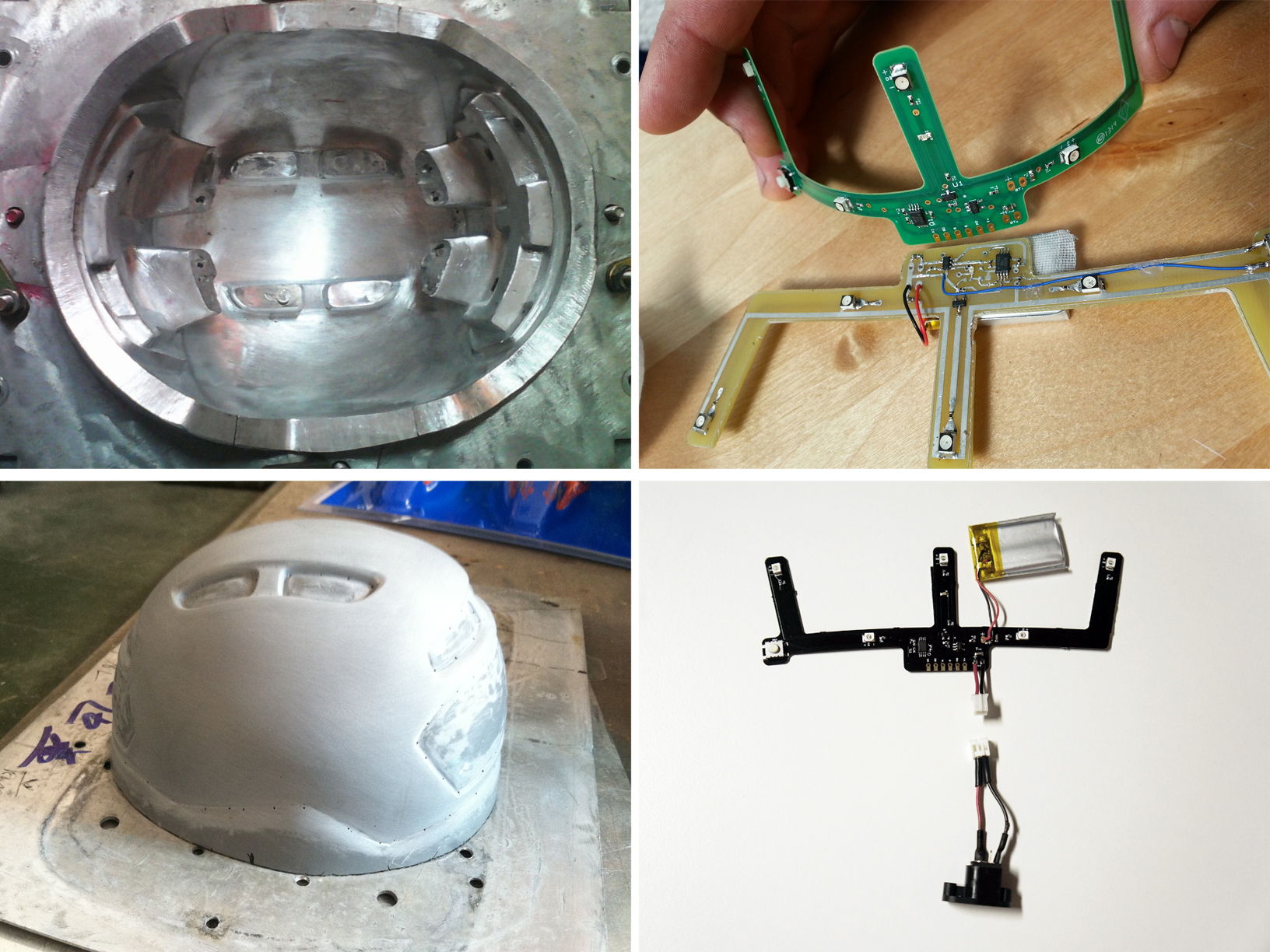
With the vacuum forming, EPS and lens tooling complete I was set to travel to my manufacturer in China to review samples, write assembly procedures with the finalized circuit boards, and crash test the first few samples! This was a very long, educational and anxious week for me. We finally crash tested the helmet directly on each battery first and the results were VERY positive. We were now set to begin production.
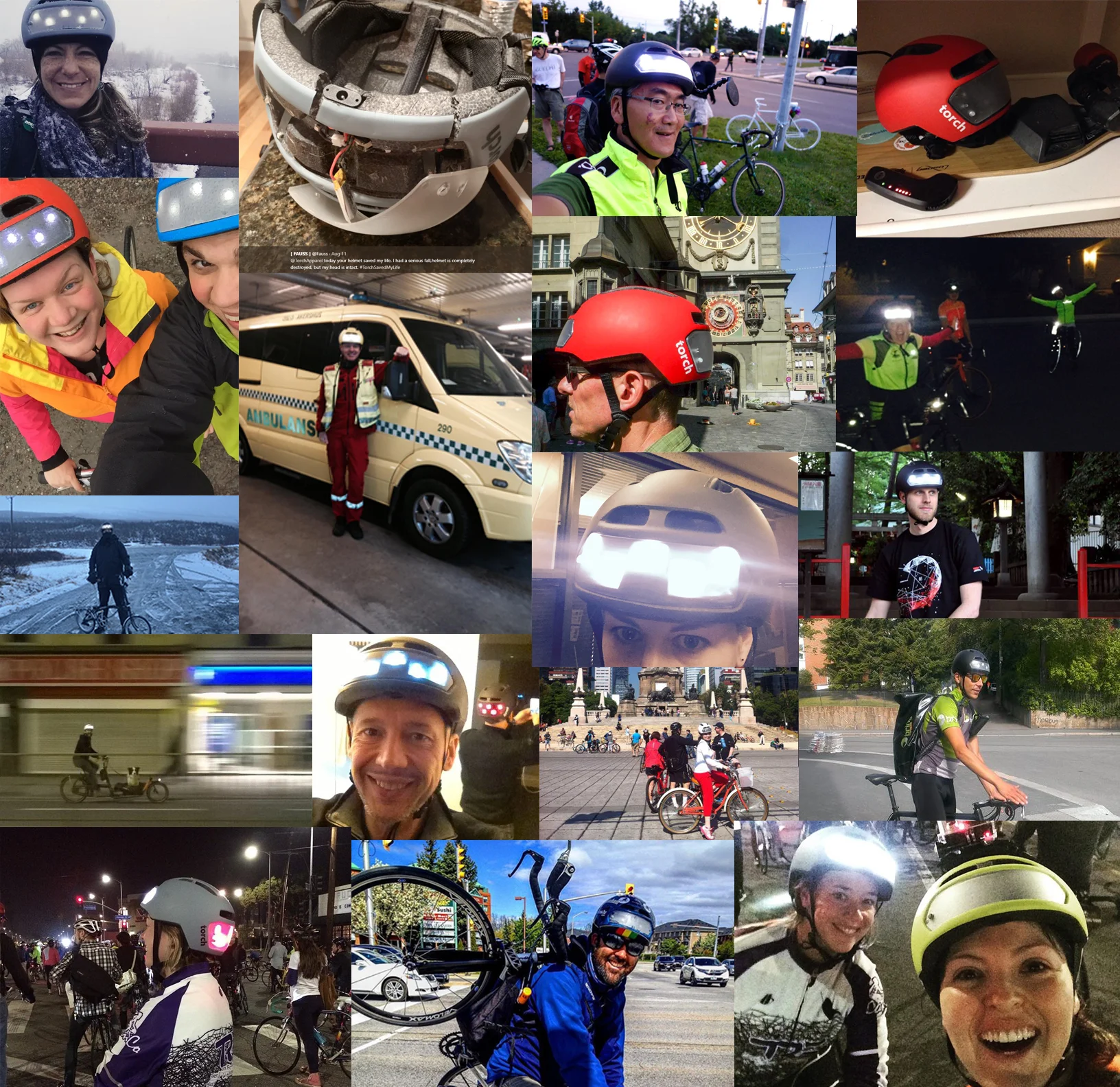
After shipping helmets to over 50 countries we continue to receive pictures, emails, tweets and so on with excited and happy customers. Many are just selfies while some are images of their helmet post crash with a message explaining how their helmet saved them from harm or worse. It's messages like these that confirm I have achieved what I had set out to do.
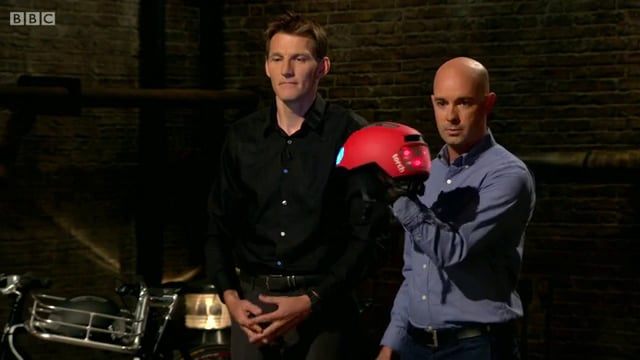
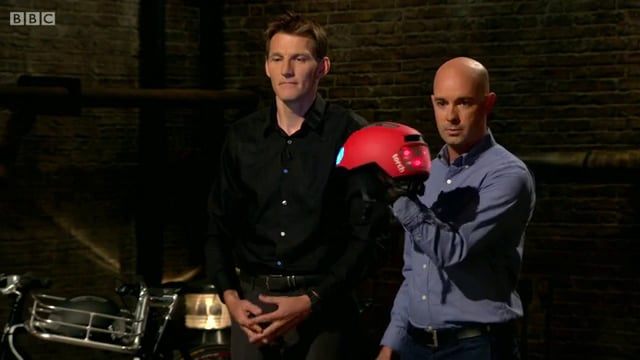